SULFURIC HARD ANODIZE TYPE III
” HARD COAT “
Meets and complies with all import & export environmental regulations (RoHS).
Sulfuric Hard Anodize: MIL-A-8625 Type III Class 1 is commonly referred to as “Hard Coat” and produces a much harder, thicker oxide coating then regular anodize. These coatings are generally used when a more structurally durable finish is desired, including improved abrasion resistance, corrosion resistance and hardness.
The Type III Class 1 non-dyed oxide coating will produce various shades of color from a light olive hue to a dark gray based on type of aluminum alloy and processing time, current density and temperature. Desired parts can be masked to prevent coating buildup. These masked surfaces also can be coated with a conversion process referred to as MIL-C-5114. We offer chromate conversion and non-chromate conversion to meet RoHS requirements.
Sulfuric Hard Anodize: MIL-A-8625 Type III Class 1 is commonly referred to as “Hard Coat” and produces a much harder, thicker oxide coating then regular anodize. These coatings are generally used when a more structurally durable finish is desired, including improved abrasion resistance, corrosion resistance and hardness.
The Type III Class 1 non-dyed oxide coating will produce various shades of color from a light olive hue to a dark gray based on type of aluminum alloy and processing time, current density and temperature. Desired parts can be masked to prevent coating buildup. These masked surfaces also can be coated with a conversion process referred to as MIL-C-5114. We offer chromate conversion and non-chromate conversion to meet RoHS requirements.
INDUSTRAPLATE CORP.
ANODIZE TYPE III CAPABILITIES
Formed thickness 0.001 to 0.003 in.
Setup/Rack system
Masking for selective surface areas
Organic dying capability
Salt spray corrosion testing
Thickness, coating weight
Taber abrasion test
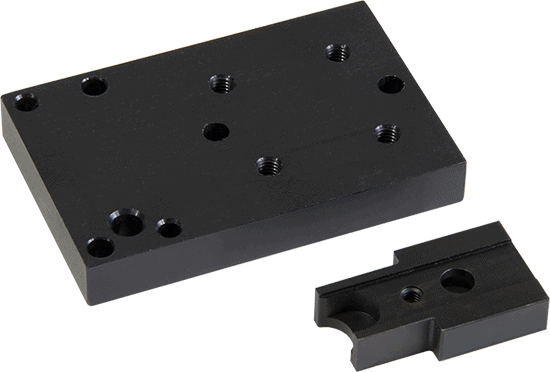
The Hard Anodizing process penetrates the aluminum substrate as much as it builds on the surface. The term “thickness” includes penetration and buildup. Typical coating thickness ranges from .001 to .002 mils. These protective finishes may also be used as base layers for other coatings such as Teflon, paint, epoxies or other adhesive materials. Hard Anodize Type III Class 2 specifies organic dying to the oxide coating. These dyes also come in a variety of colors and when applied become part of the oxide layer. Generally these thicker, harder oxide coating can be difficult to dye based on the hardness and more compacted cell diameters of the coating.
GENERAL HARD ANODIZE APPLICATIONS
Aerospace/Aviation
Applied for durability, corrosion and longevity, Rotors, Hydraulics, Pistons, Cylinders.
Automotive
Wear resistance, Pistons, Cylinders, Brake Calipers, Cams, Gears, Valves, Fuel Tanks, Hydraulics.
Electronics
High Dielectric Properties, Wear Resistance, Solar Panels, Photo Equipment, GPS Devices, Connectors, Computers Etc.
Food Manufacturing
Non Stick Surfaces, Wear Resistance, Pump Components, Icemakers, Processing Equipment, Packing Equipment.
Industrial Manufacturing
Abrasion and Wear Resistance, Corrosion Properties, Machine Components, Measuring Equipment, Robotic Components.
Medical/Pharmaceutical
Excellent Wear Properties, Repeated Sterilization (Autoclaved), Regulators, Blood Devices.
Military/Marine
Wear Resistance, Corrosion Resistance in a Salt Environment, Firearms, Guidance Systems, Robotics.